The Right Treatment, the Right Process, the Right Steel for the Job
When you’re discussing various grades of steel, the temptation is to think of the large, old time foundries with huge smelting pots full of yellow and white hot metal being poured into castings. In truth, however, the use of heat on metals has a far greater effect than simply making it malleable and it greatly depends on what you want to use your metal for that dictates any heat treatments.
It’s important to remember that steel isn’t so much one material as a name for a varied number of different iron-based metals. The number of different types is quite remarkable and depending on what’s the final steel is meant to be, the use of heat can greatly affect its hardness, strength and resistance to wear.
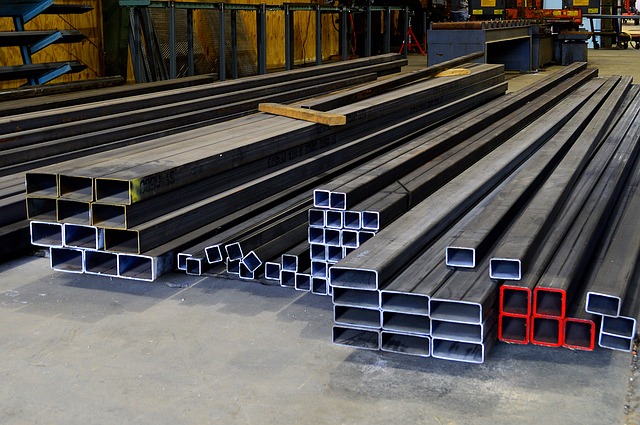
Steel in machinery has to put up with many different forces, from tension (pulling), compression (squashing), torsion (twisting) and shear (putting up with a scissor like action). Sometimes steel will be subjected to a number of different forces, meaning that it becomes a balancing act of getting the right steel that can cope with multiple stresses at once. Interestingly, this is why steel girders tend to be “I” shaped; a beam that’s supported at either end with a weight in the middle has a compressed top edge, but a bottom edge under tension. The excess materials in the side are actually unhelpful in keeping the beam in shape, so they’re removed and the steel treated in the classic ‘girder’ shape.
Some items, like gears or shafts have to withstand other combinations of forces, such as torsion and physical wear. A driveshaft that can’t withstand being in contact under torsion would be of very little use. The use of heat to create ‘case-hardened’ metals is one example of preparing the material to withstand these forces. Case hardening is using heat to create a hard, tough shell on the outside of the material, but keeping the interior softer – which means the outside won’t grind away easily but the softer inside can absorb impact and pressures without cracking or splitting.
High speed steels are another example of using heat to temper the final metal. Products like drill bits, cutting disks or blades are subjected to lots and lots of heat, thanks to friction, meaning that they need to withstand both physical pressure, sudden rises in temperature and the effects of wear to maintain sharp, clean cutting edges. High speed steels take a lot of heat to create the final product and grades can now use lasers or electron beams to impart the necessary energy onto the surface.
When we think of heating steel, it’s not just to allow it to be shaped or filled, it’s a very careful process that needs a lot of prior thought as to the chemical make-up of the steel, its final use and the types of load, stress or physical force it’s going to be under, which is one of the things that makes steel so fascinating.