What Is Tool Steel?
It’s been several hundred years since the question “What is in a name?” was introduced into the British consciousness. It’s an interesting principle, because sometimes a name is very precise and exact and at other times, it covers a broad group of items or ideas.
Metallurgy is no more or less guilty of this than any other industry, and use of the term ‘tool steel’ is used as a purely descriptive measure that covers a large number of grades.
Tool steels are high-quality materials that have very precisely controlled chemical compositions and processes to make them ideal to the particular job they do, which can be anything from forming, moulding, forging to die casting. Tool steels are required because lower grades don’t offer anything like the necessary characteristics such as durability, strength, resistance to corrosion or the ability to work in extremes of temperature or depth.
The very strictly controlled compositions of tool steels means that regardless of the purpose, making them stronger, harder, more resistant or more durable will in turn increase a number of benefits, all of which offer much greater gains when compared to ‘lower’ grade steels which could fracture, warp or even grind away under the requirements of being used in such heavy conditions.
By alloying together and controlling the product, it’s possible to make tool steels lighter, which reduces any unnecessary strain on the component parts of the final machine. The parts made can also be more precise, smaller and more reliable, which reduces the requirement for such regular maintenance. Reducing maintenance is always desirable as it reduces downtime, in turn increasing productivity and therefore, profitability.
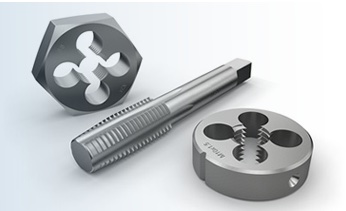
Other inclusions into tool steel include cobalt and nickel, which are used to improve hardness in high-speed steels and toughness respectively. Manipulating the elemental composition in small degrees can change the performance and other characteristics and in carbon tool steel.
Although tool steels are a highly specialised area and a very strictly controlled product, the very fact that they exist allows us to create machinery that has much greater capabilities of working in stressful conditions beyond lesser grades. It does mean that although the idea that there’s a proper tool for every job is universally accepted, sometimes people don’t consider what that tool is made of, meaning that in actual fact, there’s a proper material for every tool for every job! Sometimes, that proper material is actually very special and impressive.